Evolution
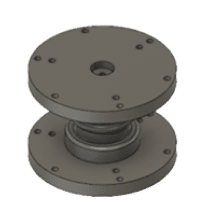

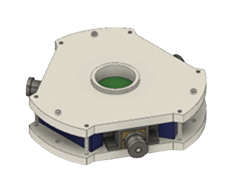

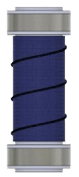

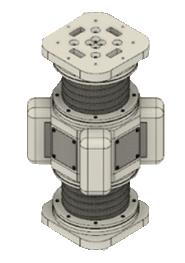
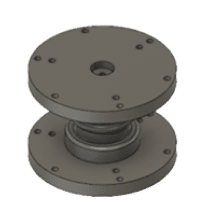
Model 1
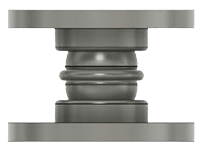
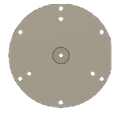
The first model consisted of two disks connected by a joint. This was the initial attempt to create a robotic body. Flexible manipulators served as the inspiration for building this model.
Model 1 was intentionally not equipped with a drive unit or control system, as it was primarily designed to research the concept of drive construction. This model assumed movement in three planes.
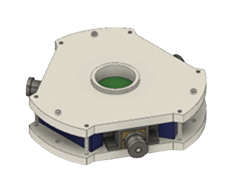
Model 2
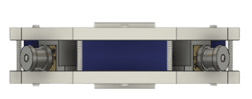
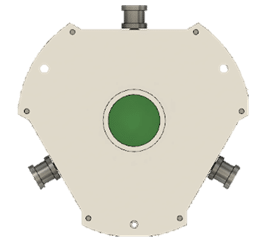
The success of Model 1 led to the design of a test version. This robot, equipped with three servomechanisms, connected with similar robots via a joint. Movement was enabled by cables connecting the robot's body to the servomechanism's shaft. However, the design's drawbacks turned out to be:
- the need to control cable tension as the sole mechanism for position control
- uncontrolled rotation of the disks relative to the joint
- complex method of connecting robots
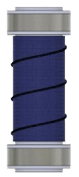
Model 3
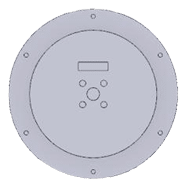
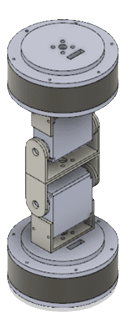
The drawbacks of the previous models were eliminated in the implemented drive, which featured:
- easy achievement of desired deflection
- no need for position monitoring
- simple module replacement
However, this model did not provide an optimal solution. Its main disadvantages were:
- complex connection method
- lack of feedback
- specific requirements regarding module arrangement and the risk of tube damage.
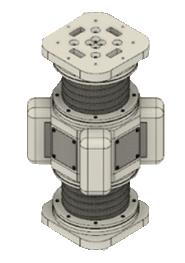
Model 4
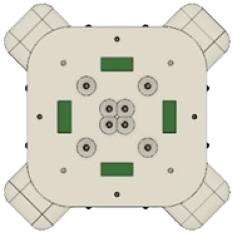
Previous imperfections were fixed by:
- shortening the tube(136mm->54mm)
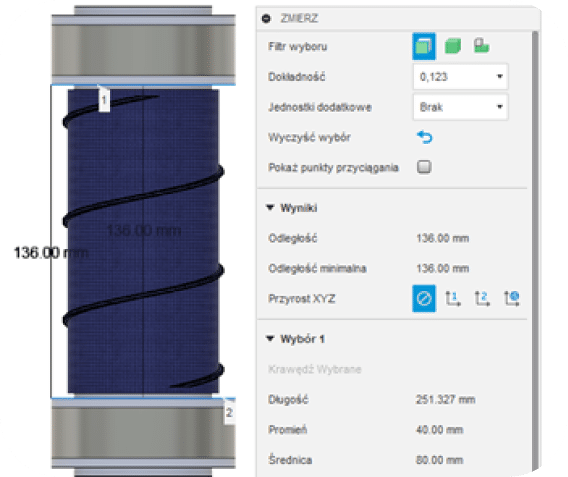
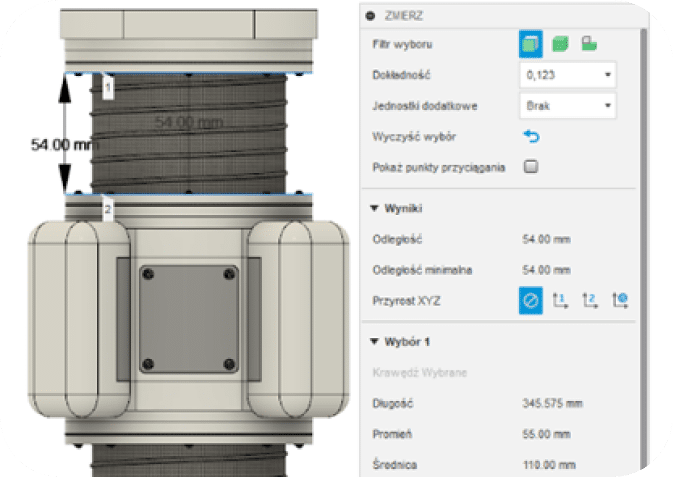
- using only one servomechanism per tube
- using end connectors
Additionally, by replacing the system of connected servomechanisms with a setup where they are separated by end connectors, the robot connection time was significantly reduced.